Last week, Elon Musk, CEO of both Tesla and SpaceX, announced new options and trims for Tesla’s award winning electric sedan, the Model S. One of the new option is a battery pack electronics upgrade, the Ludicrous Speed Upgrade, which enables faster acceleration for the existing Model S P85D and the new P90D. On this new driving mode, the Model S can accelerate from 0 to 60 mph in 2.8 second, making the 5,000 lb 4-door sedan faster than a McLaren F1.
Earlier this year, we wrote about SpaceX transferring some technology and welding equipment to Tesla. Now it seems like the new “Ludicrous” upgrade might have been made possible due to knowledge acquired through rocket engine manufacturing at SpaceX.
The Ludicrous upgrade consists of 2 improvements to the electronics of the Model S’ battery pack. The first improvement is the replacement of a standard fuse to an “advanced smart fuse” which enables the monitoring of current to the millisecond, and makes it possible to cut the power with “extreme precision”.
The second improvement is where SpaceX’s expertise might have come into play. Tesla replaced the main pack contactor to use Inconel instead of steel. Inconel is a space-grade superalloy well suited for extreme high temperature environments. This superalloy is primarily use in the aerospace industry, and one of its more famous use is in the novel manufacturing process of SpaceX’s SuperDraco engine.
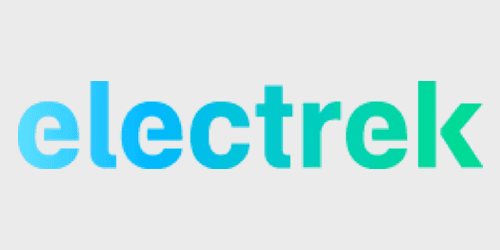
The SuperDraco at the unveiling of the Dragon V2
The SuperDraco provides trust to the launch escape system of SpaceX’s Dragon V2 spacecraft. It also offers deep throttling ability and has multiple restart capability for propulsive-landing.
Here are eight SuperDraco engines at work during a pad abort test:
Together, these eight SuperDraco engines produce 120,000 pounds of axial thrust, which is quite impressive, but maybe even more impressive and where the synergy with Tesla might come into play, is how SpaceX manufactures these engines.
SpaceX 3D prints the engine’s combustion chamber in Inconel using a process of direct metal laser sintering – a first in rocket engine manufacturing.
Here’s an Inconel combustion chamber emerging from a 3D metal printer at SpaceX:
Inconel is a difficult (read expensive) metal to shape and machine. The ability to 3D print it streamlined the manufacturing process, presumably making it less expensive. Inconel works well under incredibly high temperature, which is the reason why it’s being use to build rocket engines, but it is also why Tesla chose the superalloy for its new main contactor. Inconel is more “springy” than steel under the heat of heavy current, which combined with the “smart fuse” allow Tesla to increase the max power output of the Model S’ battery pack from 1300 to 1500 Amps.
It’s unconfirmed if SpaceX had any involvement in Tesla’s development of the new Inconel main contactor or if it was a similar transfer of technology and equipment as it was with stir welding. A Tesla representative didn’t respond to inquiries on the subject.
Aside from stir welding, sharing a CEO (and the CEO’s jet) and now possibly the use of Inconel, SpaceX seems to have also involved Tesla, to a lesser level, in their plan for a space-based internet service through a constellation of satellites. The company revealed through an application with the FCC that they intend to install a test ground station for their satellite constellation at Tesla’s Fremont factory.
Some people are speculating that SpaceX’s broadband internet could eventually replace the current internet service in Tesla’s cars, which is currently transitioning to LTE, but there are doubts about the feasibility of this project.
No matter the level of synergy between Tesla and SpaceX, any link between the manufacturing of spacecrafts and consumer vehicles is too cool not to mention.
Pictures courtesy of SpaceX.
FTC: We use income earning auto affiliate links. More.
Comments