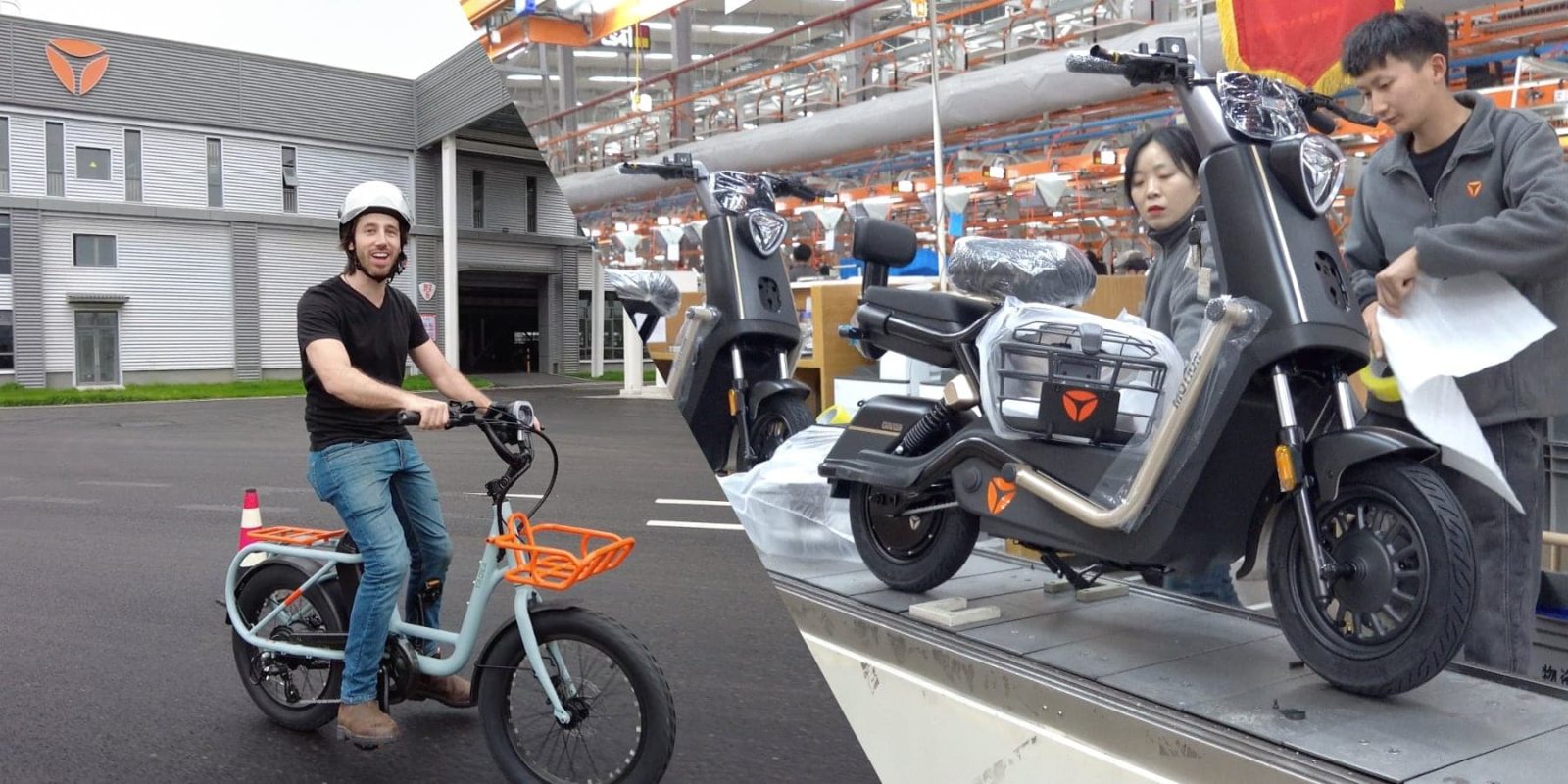
I recently took a trip to China, where I had the opportunity to visit one of Yadea’s several global factories used to produce a wide range of light electric vehicle models and styles. As the world’s largest electric vehicle manufacturer, it was a chance to see how the most popular forms of EVs – namely e-bikes, e-scooters, and electric three-wheelers, are built in sophisticated factories featuring high-level quality control processes. The experience was thoroughly eye-opening, and blew my expectations away!
In fact, one of the biggest surprises of my time at the factory was just how much effort is put into quality control along the way. It was a magnitude that, frankly, I was surprised to see.
I don’t mean that as a slight. It’s just that, like most people, I was probably a bit misinformed before this trip. The term “Chinese manufacturing” makes most of us in the West think of cost reductions and competitive pricing – not heavily automated manufacturing and multi-tier quality assurances. But with Yadea’s massive size has come the opportunity to deeply invest in the hallmarks we previously associated with a bygone era of Western manufacturing.

And I’m not exaggerating when I refer to Yadea as “massive.” This was just one of eight global factories, and this one spanned over 1,000 acres (that’s around 750 American football fields). And this is just Phase I of the factory, which was only built a few years ago. Phases II and III are going to be even bigger, adding much more manufacturing capacity.
Yadea is already a household name all over Asia, where it dominates the markets for scooters, bikes, and other micromobility devices. Last year, over 16 million two-wheeled EVs rolled off the company’s production lines. Yadea refers to itself as the world’s largest electric motorbike manufacturer, but it is also the second-largest motorbike maker, period. With 16M annual production volume, that puts the company within striking distance of overtaking Honda’s 18M annual units. And that’s even more impressive considering Yadea exclusively produces electric vehicles, unlike Honda which nearly exclusively produces combustion engine motorbikes.
Yadea now has a growing presence in Europe and has recently set its sights on a major expansion into North America. That means that Americans are set soon to get access to some of Yadea’s impressively designed and built light electric vehicles (though mostly starting with lighter electric bicycles and scooters).
Check out my video below to see inside Yadea’s factory yourself and to join me for my test drives on several of Yadea’s e-bikes, e-scooters, e-mopeds, and e-trikes. You’re not going to want to miss it!
My tour started in just one corner of the sprawling Jinzhai factory, where I watched as rows of plastic injection molding machines worked in rhythm to pump out various scooter-shaped bits and pieces. This is where many of the body panels, shrouds, and other molded components of Yadea’s electric scooters and e-mopeds are produced. Many smaller companies outsource the production of these types of components, but Yadea does it all in-house to maintain better control over the processes and thus the quality of the parts.
The machines run largely autonomously, though a few workers monitor the machines and can respond to any area, if necessary. I poked my head into a few of the lines and saw some machines churning out recognizable parts like shrouds around the handlebar displays and cargo areas under moped seats, with each completed component moseying down a conveyor belt towards a finished parts pile.
The building was massive and already housed 24 injection molding machines, each the size of my college dorm room. However the area of the building that was currently storing stacks of just-produced parts was already taped off with sections where more injection molding machines would soon be installed. They told me that there are plans to operate 60 of these massive machines here. Yadea continues to roll out new EV models and increase its sales around the world, and that means it is always ramping up its own internal component production capacity to match.
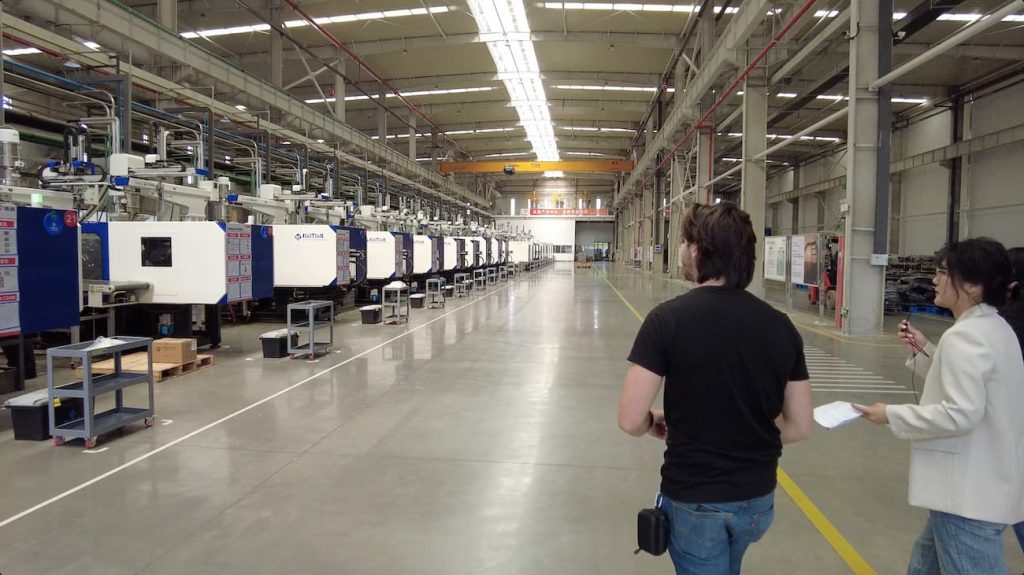

From there we hopped aboard a cute little electric shuttle bus and moved to another building in the complex where welding takes place.
This particular welding building was set up for Yadea’s three-wheelers, which are basically the lightweight farm trucks of China. In the same way you see a bunch of clapped-out F-150 pickup trucks all over rural America, you see these electric three-wheelers all over rural China. That’s why, despite Yadea’s scooters and mopeds being built largely for both the domestic and international markets, their three-wheelers are pretty much only sold in China.
I think they could be incredibly powerful utility vehicles in the US, but that’s another issue for another article. For now, I got the chance to see how these local versions of a pickup truck are made. And I was surprised by just how automated the production is.
Robotic welding seems to take care of most of the fabrication, with the vehicles going from steel tubes and sheet metal to mostly formed trikes without ever touching the ground. Laser cutting ensures each raw sub-component is cut to the exact right size and has smooth finished edges. The pieces are passed from machine to machine, sometimes by robots and sometimes by human hands, until full frames come out the other side.

When the frames are finished being welded, multiple steps of electrophoresis for corrosion resistance and then robotic painting await the finished pieces.
I wasn’t able to go through the actual painting area because it’s closed off to ensure a clean environment for the robotic painting machines, but I did get to see the massive environmental protection equipment that filters the air leaving the painting section of the factory, ensuring that any harmful emissions from the aerosolized paint and treatment chemicals are scrubbed and don’t just get pumped out into the atmosphere.
Again, I definitely went into this tour with some preconceptions that turned out to be false. That doesn’t mean there isn’t polluting heavy industry in some areas, but modern factories like Yadea’s take great pains to reduce emissions. The air around the factory was perfectly clean, the grass was greener than my grass back home, and the courtyards around the building were so nice I would have sat and had a picnic in them if there was time. The effort made to create a clean and comfortable work environment pays dividends now and into the future.
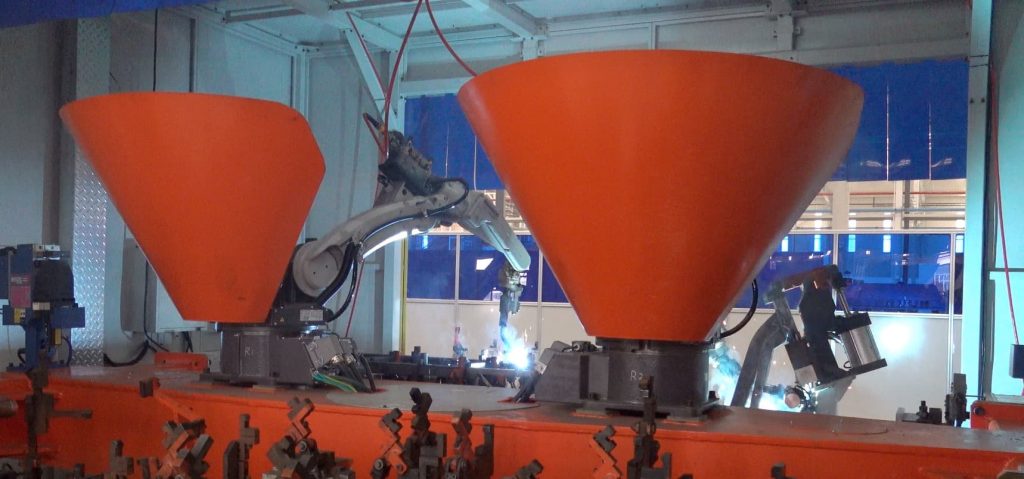
Next, we moved on to yet another massive building in the factory complex, this time where assembly of several different electric scooter and e-moped models takes place. It’s a bit hard to gauge scale inside these huge buildings, but I’m told the building was around 450,000 square feet, or roughly 10 acres. It had a legit football field inside of it, but more on that in a moment.
There were 18 assembly lines in the building, each producing a different model of e-bike, e-scooter, or e-moped. Racks of frames that have been welded in another part of the factory roll in at one end of each production line, where they are scanned and loaded onto the line. The bare frames move along the line as workers install all of the components.
In a matter of minutes, the empty frames receive their motors, controllers, batteries, wiring, lights, body panels, seats, and more. A ballet of suspended racks of components automatically lower themselves from the ceiling at precisely the right location for workers to pluck the parts from the air and install them on the scooters. Everything is designed to be as efficient and comfortable as possible, with very little need to bend over or strain.

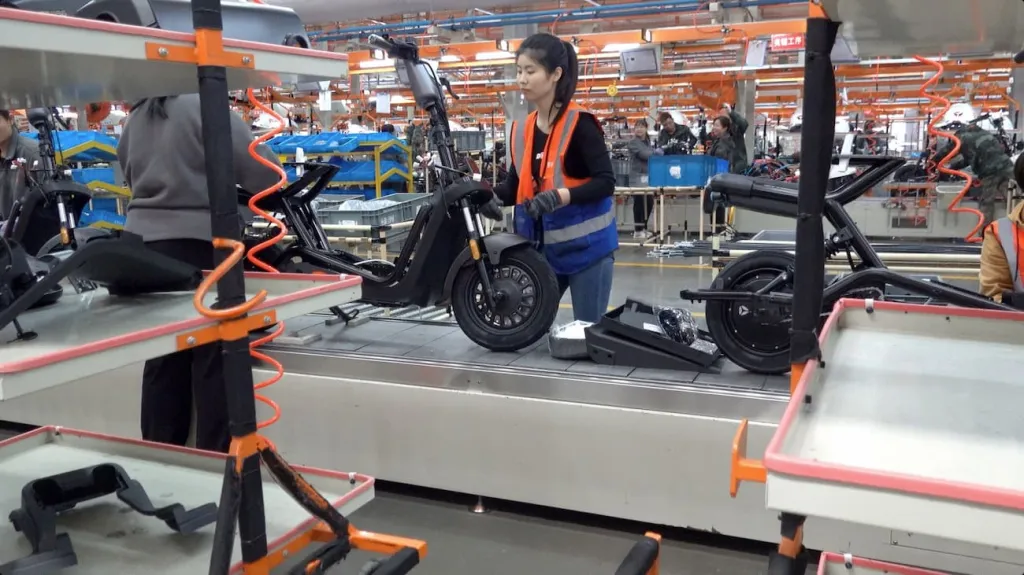
From what I could tell, a new electric bike rolled off the line around once every 25-30 seconds or so, while an electric moped rolled off the line every 40 seconds.
It looked like it took around 20 minutes for a bare moped frame to work its way down the assembly line and roll off the ramp at the end as a fully functional electric scooter.
The three-wheelers seem to take longer, with one e-trike rolling off the line around every five minutes.
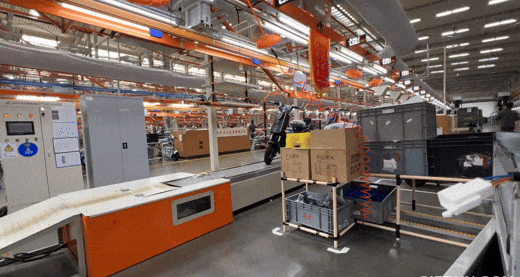
From there, still, more workers receive the scooters and begin going through a several dozen-point inspection to ensure that everything has been assembled correctly and all of the scooter’s functions are working properly. Things like wheel alignment, torque spec, electrical connections, lighting/sound levels, and many other important areas are all examined as part of the end-of-line quality inspections.
Once the vehicles get the seal of approval, they’re walked over to yet another aerial lift that slowly plucks them from the ground and soars them through the air to another part of the factory.
Each of the buildings is connected by a series of catwalk-style sky bridges. There, the tracks suspending the finished vehicles can pass from building to building without actually going outside. In this way, parts and vehicles can move between different areas of the sprawling complex even while it is raining or snowing.

I mentioned a football field in the middle of this factory building, and I wasn’t kidding. There’s an entire turf field in there. In fact, it used to be real grass, but that required opening the skylights for good sun exposure, which the workers said made the building quite hot in the summer. So instead, they turned it into a turf field.
It gets used for a number of different events, from playing sports on breaks to hosting company events and unveiling. When I passed through, there were several models of electric scooters still set up on the field from a recent event. You can see the field in my video at the top of this article.
There’s also a library at the end of the field, featuring around a dozen shelves of books set up in a rectangle to create a little reading room complete with tables and chairs. Workers can read the books there or they can take any books they like (there’s no charge and the books are regularly replaced by the company).

The last area I had the chance to see in the factory was a staging zone for finished three-wheelers that were ready to be trucked away to local stores (Yadea counts over 40,000 brand stores around the world). There was also a display set up showing raw materials from various stages of production, from bare steel tubes to coated frame members and painted panels. They highlighted the quality of each step, such as how the bare frame tubes are laser cut so precisely that the edges are smooth and feel like a factory edge.
Despite wearing my journalist/YouTuber hat most of the time these days, I do in fact have a mechanical engineering degree on my desk that I occasionally get a chance to dust off. As a younger man, I also spent years working as a machinist in a machine shop and I previously ran my own manufacturing operations, so I have at least a cursory knowledge of what I was looking at for each production step around the factory.
I can tell you that of all the light electric vehicle factories I’ve visited in several countries around the world, I’ve never seen an operation run more professionally than what I saw at Yadea. The attention to detail, the level of automation, and even the consideration of workers’ needs, it was all simply above and beyond anything I’ve seen before.
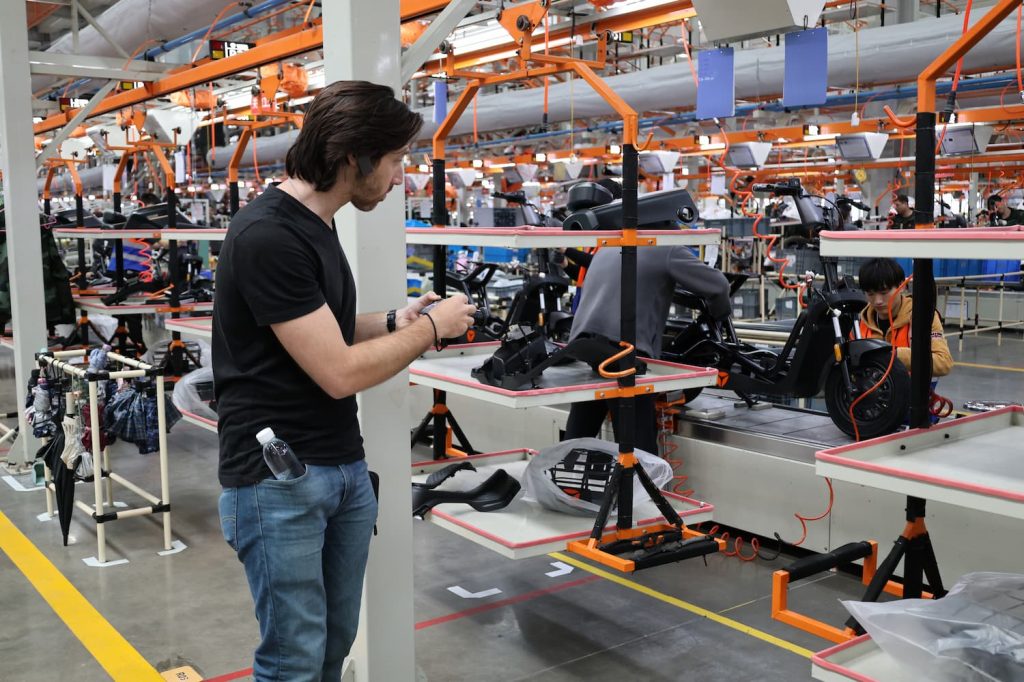
And that was all before lunch!
With the first part of the tour finished, we headed to the employee cafeteria where I got to choose whatever I wanted from a wide a la carte menu. This also surprised me.
While I didn’t expect the workers to be eating gruel, I was caught off-guard at just how good the food was! And this wasn’t some visiting guest cafeteria (many factories have VIP cafeterias off to the side, and I’ve eaten in those before). I was eating where all the factory workers eat, the people’s cafeteria, the great equalizer. And I know that because my entire lunch was spent with hundreds of people staring at me as the only white guy in the room. I definitely caught a few folks taking pictures of me. It’s cool though, I just told them I’m Keanu Reeves.

After lunch, and having already seen how and where Yadea’s vehicles are produced, I had a blast spending the rest of the afternoon test-driving most of them!
The factory tour was impressive, but it’s on the company’s vehicle testing area and proving grounds that I had the most fun! To hear how that went, you’ll have to stay tuned in for Part Two of this story, coming in another couple days (or you can just watch the video at the top of this article, which includes both parts together for a major sneak peak!).
FTC: We use income earning auto affiliate links. More.

Comments