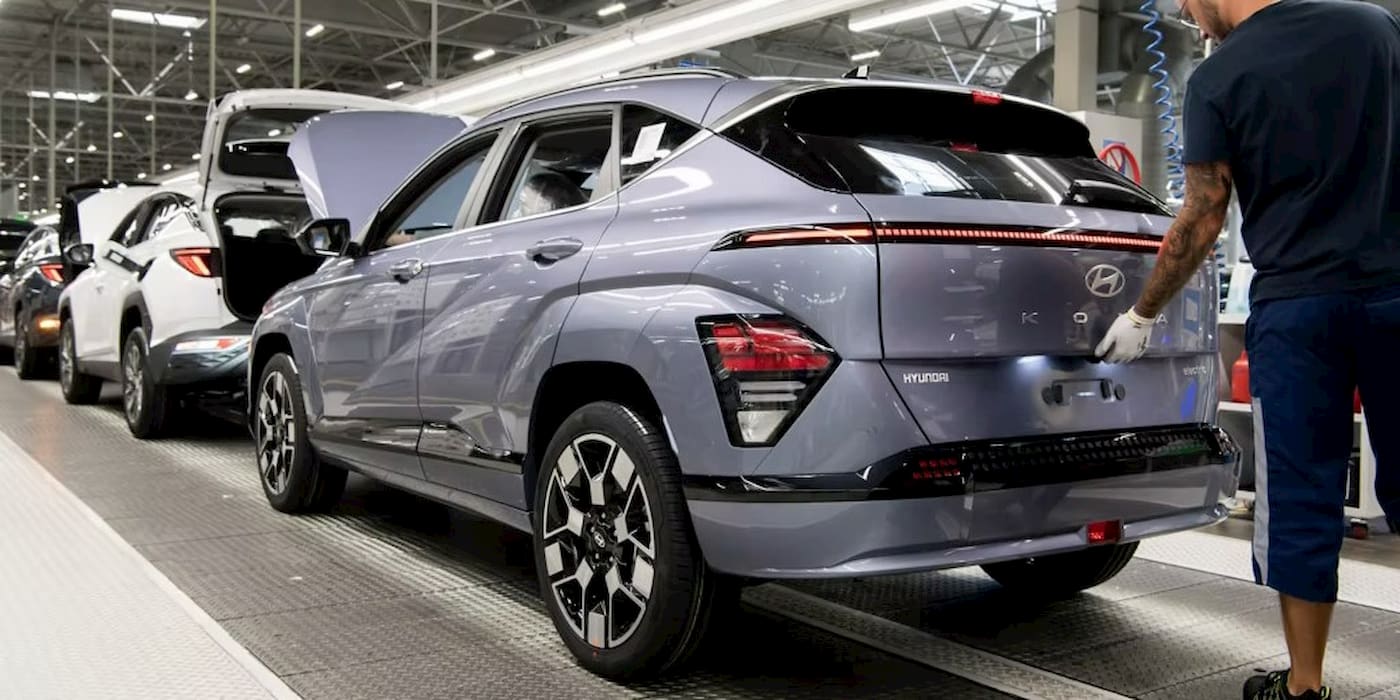
Hyundai is taking a page from Tesla as it plans to model a new EV production method after its Giga Casting. The new process,”hypercasting,” can significantly cut costs while boosting output.
According to an exclusive report from the Korean newspaper Hankyung, Hyundai’s new EV production method is inspired by Tesla’s Giga Casting.
The process involves injecting molten aluminum alloy into casting molds that harden into the vehicle’s frame. Since introducing the method in 2020 at Tesla’s Fremont Factory, the EV maker has introduced it at its plants in China and Germany.
The massive machines produce parts much bigger than what the auto industry was used to. Automakers can save much-needed time and resources without the need to bond multiple parts (it can also help reduce the vehicle’s weight). Tesla is said to have reduced costs by about 30% using Giga Casting.
Traditional methods include drilling thousands of holes in around 70 steel plates and welding them together individually. You can see how it saves time and money.

Hyundai takes a page from Tesla to boost EV production
Hyundai, which reached a tentative wage pact with its South Korean labor union Tuesday, agreed to a “special agreement for future growth.” The goal is to boost domestic investment to convert existing ICE manufacturing plants into “core manufacturing bases for future vehicles.”
Korea’s largest automaker has decided to develop its own casting, processing, and assembly plant, with production planned for 2026.
The company already filed for the “hypercasting” trademark with the United States Patent and Trademark Office on August 21, 2023.
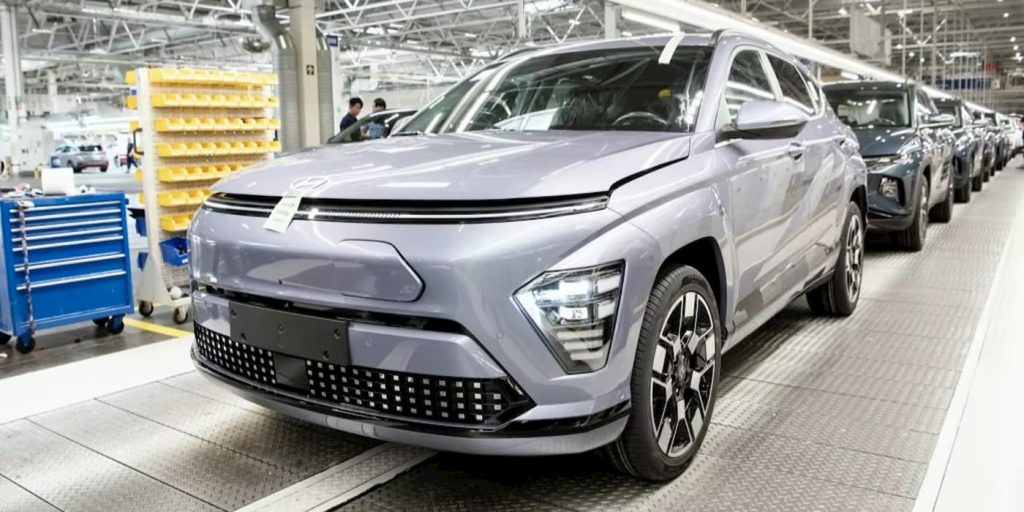
Hyundai isn’t the only one looking to take a page from Tesla to boost EV production. Several automakers, including Toyota, Volkswagen, and Volvo, are looking to introduce similar processes. China’s Geely has already introduced the method to build ZEEKR models.
The South Korean automaker is also looking to counter Tesla’s proliferating Supercharger network in its domestic market with its own ultra-fast chargers.
Top comment by brucet
"Traditional methods include drilling thousands of holes in around 70 steel plates and welding them together individually."
You don't need to drill holes in order to weld plates together.
If "thousands of holes" means just 2,000, that would mean more than 28 holes per steel plate. Seriously?
Yes, such a structure would need some holes for mounting to the frame and for attaching other parts, but never thousands of holes.
Hyundai has had success so far in transitioning into the electric era with EV models, including the IONIQ 5, IONIQ 6, and Kona Electric. However, to keep up with EV leaders like Tesla and BYD, Hyundai sees an opportunity to transform its production network.
Electrek’s Take
With Hyundai planning to convert its existing ICE vehicle manufacturing network for the electric era, why not upgrade them to optimize efficiency?
Tesla has proven the process not only works but works much more efficiently than traditional methods.
With several other automakers hopping on board, Hyundai looks to advance its position in the industry with plans to become a top three global EV producer by 2030. By then, the company expects to have 31 EVs under the Hyundai, Kia, and Genesis brands.
FTC: We use income earning auto affiliate links. More.
Comments