
Tesla has applied for a new patent that is revealing the lithium extraction process that Elon Musk vaguely described as “using table salt to basically extract lithium from ore” during Tesla’s Battery Day last year.
It could cut costs by more than 30%, according to the automaker.
During Tesla’s Battery Day last year, the automaker unveiled a lot of new technologies that it couldn’t spend a lot of time explaining.
One of those was that Tesla has developed a new lithium extraction process that Drew Baglino, SVP of engineering at Tesla, claimed would “result in a 33% reduction in lithium cost.“
CEO Elon Musk described the process in a very simple way::
“What is the best way to take the ore and extract the lithium and do so in an environmentally-friendly way? We have been looking at from a first principle physic standpoint instead of just the way it has always been done. We found that we can actually use table salt, sodium chloride, to basically extract the lithium from the ore. Nobody has done this before to the best of my knowledge.
He didn’t go into more details about the process, which raised quite a few eyebrows in the lithium industry.
But now we have obtained a new patent application for Tesla’s new lithium extraction process, which comes with a lot more details about this mysterious “table salt” method.
In the patent application called “Selective extraction of lithium from clay minerals,” Tesla describes the main problems with current extraction methods:
Lithium is a strategic metal for the lithium ion battery (LIB) and electric vehicle (EV) industry. Therefore, a means for economically extracting lithium from various lithium sources is important in order to reduce the cost of batteries and electric cars. The dominant lithium sources commonly used for mining are lithium brines due to the low cost associated with Li extraction from these brine sources. However, the ever-increasing demand for LIBs makes it necessary to explore other lithium sources.
Another method for Li extraction is to extract the Li from clay minerals. In this process, the lithium is obtained by acid leaching, where clay minerals are mixed with an aqueous solution of common mineral acids, such as H2SO4 or HCl, and then heated under atmospheric pressure to leach out the lithium contained in the clay minerals. This acid leach method not only leaches out lithium, but it also leaches out high concentrations of impurities including Na, K, Fe, Al, Ca, and Mg. High lithium loss from the subsequent removal of the impurity elements, especially Al removal, may significantly lower the overall lithium extraction efficiency. Furthermore, high acid consumption and complicated leach solution purification methods also make the overall extraction process less cost-effective and not environmentally friendly.
Tesla summarizes its own new method in the patent application’s abstract:
Processes for extracting lithium from a clay mineral and compositions thereof are described. The extraction process includes providing a clay mineral comprising lithium, mixing a cation source with the clay mineral, performing a high-energy mill of the clay mineral, and performing a liquid leach to obtain a lithium rich leach solution.
So it’s a little more complicated than just adding table salt, but the main cation source described by Tesla in the patent application is indeed NaCl, sodium chloride (aka table salt).
Tesla describes the effect of adding NaCl to the milling step of the process:
The effect of adding NaCl to the milling step of the process was measured. NaCl powders and fine clay mineral particles in weight ratios of 3:97 (i.e. NaCl to total mixture (i.e. NaCl + Clay) = 3%; and corresponding to a Na:Li molar ratio of about 2.7:1) were weighed and placed into a PM100 planetary ball mill and continuously milled for up to 3 hours at 500 rpm rotation. The ball-milled NaCl/clay mixture was then collected and transferred into a glass reactor for water leaching. 31 gram of the NaCl/clay mixture was loaded into the reactor with water added to create 150 gram slurries with salt/clay mixture to water weight ratios of 1:4 (i.e. a 20 wt.% salt/clay mixture loading in water). Once the slurry is created, water leaching is performed at 90oC under 1000 RPM agitation for up to 20 minutes. A condenser is used to minimize the water loss during leaching. Following a subsequent filtration using 5 um filter paper, the leach solution was collected for further chemical composition analysis.
The results of the chemical analysis from adding NaCl:
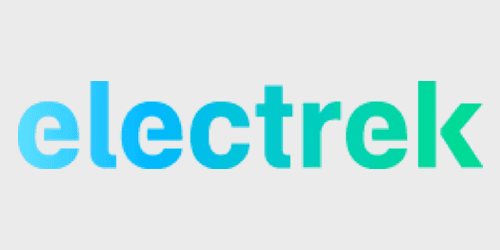
Obviously, there’s a lot more to the new extraction process, and if you want to get into the nitty-gritty, here’s the full patent application from Tesla:
[scribd id=515006322 key=key-9UUh8P8HuupCCBtAHJNF mode=scroll]
What’s also exciting is that Tesla plans to use this new process itself on its own new lithium claim deposit in Nevada that apparently consists of over 10,000 acres.
FTC: We use income earning auto affiliate links. More.

Comments