
At its Battery Day event, Tesla unveiled its new 4680 battery cell developed in-house and the manufacturing process behind it.
The highly anticipated presentation went deep into details about all the different pieces of material science, design, and manufacturing innovations that it took to deliver the masterpiece of a puzzle that the automaker needed to put together to reduce battery costs by more than 50% in just 3 years…
Over the last few years, Tesla has been making a lot of moves related to batteries.
We are talking about buying companies like Maxwell and Hibar, and applying for patents on new technology, like a tabless battery cell and a cell to pack design.
While all these moves were mostly evaluated on their own merits, it wasn’t clear how all those things would fit together.
That’s exactly what Tesla demonstrated at its Battery Day.
Tesla explained how they have made major improvements in five key aspects of batteries:
- Cell design, specifically form factor.
- Battery cell factory design with manufacturing innovations
- New anode materials
- New cathode materials
- New battery pack design
And then, by combining all these things together, Tesla achieves a battery cost breakthrough with a 56% reduction in cost per kWh:
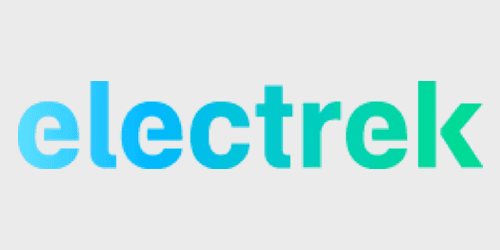
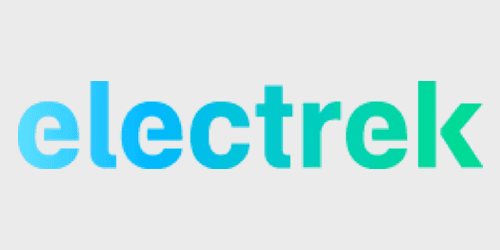
What is most impressive is how all those innovations work together. Each result in an incremental improvement to battery technology, but if you combine them together, you get breakthrough-level performance and cost:
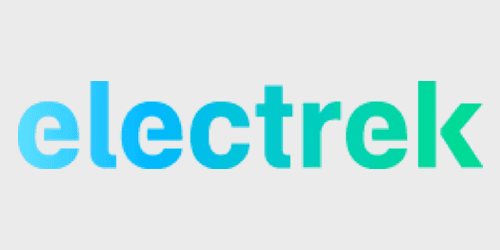
At the cell level, Tesla did something quite simple: make the cell bigger.
However, when you make a cylindrical cell bigger, you run into thermal problems, but Tesla managed to address those by designing a tabless cell with much less resistance.
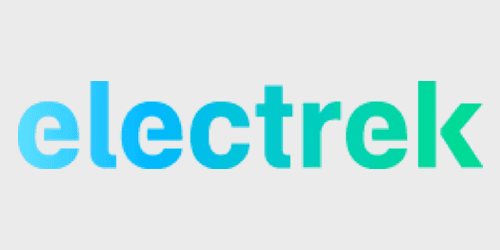
You can read more on the new Tesla 4680 battery cell in our previous report about it.
The new cell design is also simpler to manufacture and requires less capital investment to bring to production.
But of course, Tesla didn’t stop there.
The company looked at the entire manufacturing process of battery cells. That’s Tesla’s Roadrunner project that we have been talking about over the last few months.
Several improvements were implemented, like dry coating electrode manufacturing, a process that Tesla acquired through its acquisition of Maxwell::
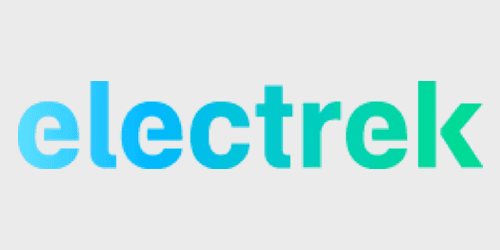
This powder into film process is wildly less complicated and requires less machinery than the usual wet process to create an electrode.
CEO Elon Musk noted that the process is still “not totally working, but it is close to working.”
Tesla has had to improve on Maxwell’s proof of concept and turn it into an actual production-ready system.
But the end result is a dramatic improvement in footprint and energy required to produce the electrode:
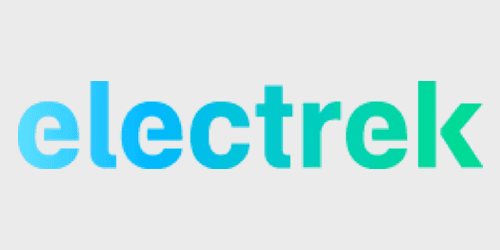
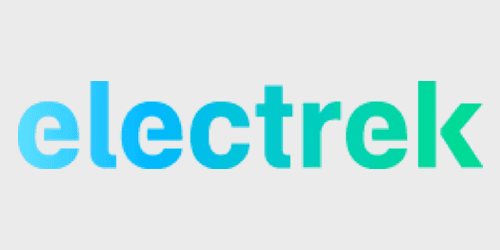
Ultimately, that also results in a cost improvement at the battery cell level.
At the assembly level, Tesla redesigned all the machines to achieve a super high-speed assembly process that can deliver seven times the output per line than what is currently done:
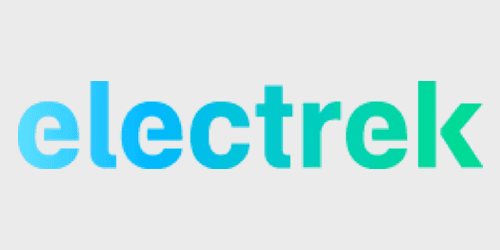
Tesla has also made other incremental improvements to the winding and formation processes, resulting in what they believe is a total 18% reduction in overall battery cost through the manufacturing process redesign.
At the chemisty and material level, Tesla has also announced some important improvements.
The company claims to have designed a new silicon that is going to be much cheaper than current solutions:
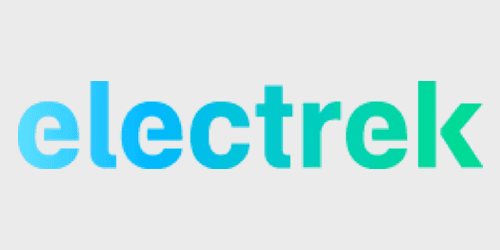
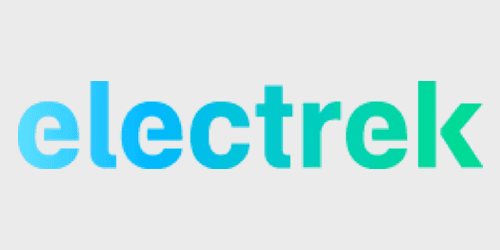
Tesla believes that the improvement to the anode will result in a 5% reduction in cost per kWh for the battery.
For the cathode, Elon Musk and Drew Baglino claim that Tesla redesigned the entire production process based on a first principle approach.
Without going into the details, they say that they eliminated the wastewater and are able to transform the nickel into a cathode much more efficiently:
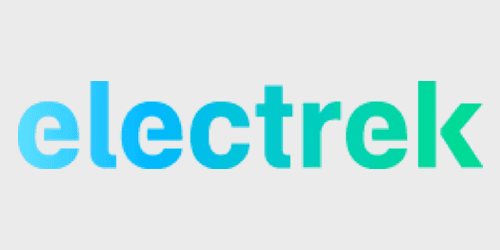
The automaker plans to deploy its own cathode manufacturing facilities based on this process.
They believe that it will result in an even greater reduction in cost per kWh than the new anode with a 12% drop.
Tesla now aims to ramp up the battery production to 10 GWh at the pilot plant in Fremont within about a year.
After that, they want to deploy the new production system at a larger scale, and they are aiming for 100 GWh by 2023 and 3,000 GWh by 2030.
Finally, Tesla announced that it is also integrating those new battery cells inside its vehicles differently.
Inspired by the aerospace innovation of building airplane wings as fuel tanks instead of building the fuel tanks inside the wings, Tesla decided to build a battery pack that acts as a body structure, linking the front and rear underbody parts.
The result is quite elegant:
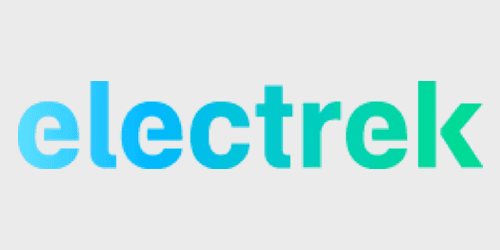
They call it a “structural battery,” meaning that the battery is not just an energy device but an actual structural part of the vehicle.
It was also achieved through Tesla building expertise in large casting, first through the rear underbody of the Model Y and through Tesla’s material science team that has been developing new alloys that enable the larger casting.
They believe that the new design reduces overall vehicle mass by 10% and increases range by 14%.
Electrek’s Take
Everything Tesla unveiled here is impressive. Halving the cost of batteries believed to be at around $110/kWh for Tesla currently would put Tesla at around $50 per kWh. That means a 50kWh pack for the $25,000 car would only cost Tesla $2,500. That’s a tenth of the cost of admittedly larger batteries that went into the original Model S.
It’s like a very complex puzzle that they managed to put together by not only looking at the bigger picture but also by being willing to discard the existing puzzle pieces and engineer their own from the ground up.
You can tell that the whole thing took an incredible amount of work from Tesla.
Kudos to everyone involved, but it looks like the work is far from done. Now Tesla needs to deliver.
While I was impressed during the presentation, there was a lot of talk about not having completely figured out everything.
Tesla is still a year away from completing even just the pilot plant — though to be fair, at a planned capacity of 10 GWh, it’s not really pilot plant volume.
That’s more capacity than most battery factories in the world today.
It’s likely going to take a while until we can fully appreciate everything that Tesla announced at Battery Day.
FTC: We use income earning auto affiliate links. More.
Comments